Food & beverage webinar
Validating your CapEx projects to avoid unnecessary expenses
On-demand Webinar now available!
45 minutes
What would it mean for your bottom line if you could defer, reduce or entirely avoid that next big capital project by maximizing existing assets instead?
Food and beverage manufacturers’ resources—capital, labor, and time—are already squeezed, so it is critical that your investment decisions are the right ones.
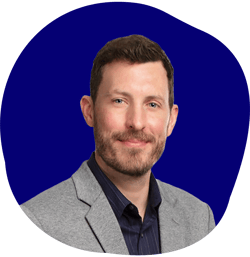
Tony Moses, PhD
Fellow - Product Innovation
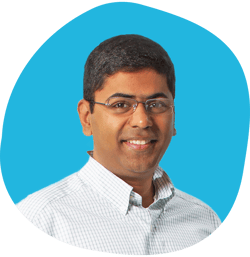
Niranjan Kulkarni, PhD
Sr. Director Consulting Services
About the webinar:
Food and beverage manufacturers’ resources—capital, labor, and time—are already squeezed, so how are you ensuring your investment decisions are the right ones? In this 45-minute webinar, Tony Moses, PhD, Fellow of Product Innovation, puts this topic to our resident Lean Six Sigma Master Black Belt, Niranjan Kulkarni, PhD, with questions on common operational challenges that regularly lead to hefty capital expenses.
The duo runs through real-world examples and case studies of capital cost avoidance that might actually make your jaw drop. Imagine shifting from investing in a whole new packaging line to simply altering your schedules, or getting to the root of a malfunctioning piece of equipment’s problem so you no longer need to replace it years ahead of schedule. That’s the power of validating your CapEx projects. Kulkarni walks through how he leverages data and simulated environments for these validations to explore alternative solutions to meet your desired operating goals—which often translates to major cost avoidance.
The webinar concluded with a live Q&A.